Intalox saddle packing manufacturing involves a series of precision processes tailored to different materials (ceramic, metal, plastic), each designed to ensure structural integrity, dimensional accuracy, and performance consistency. The production methods vary based on material properties but share core goals of achieving the characteristic saddle shape and functional efficiency.
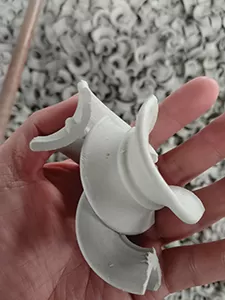
Ceramic Intalox Saddle Manufacturing
Ceramic production begins with raw material preparation. Alumina powder (with purity ranging from 70% to 99% based on grade) is mixed with binders (e.g., clay, organic adhesives) and water to form a homogeneous paste. This mixture is then shaped using isostatic pressing or extrusion molding: isostatic pressing uses uniform pressure (100–200 MPa) in a flexible mold to form the saddle shape, ensuring dense and uniform structure; extrusion molding pushes the paste through a die with the saddle profile, suitable for mass production of small to medium sizes. After shaping, the green bodies undergo drying at 80–120°C to remove moisture, preventing cracks during sintering. The critical sintering step occurs in high-temperature kilns at 1500–1700°C, where particles bond tightly, and the ceramic achieves its final hardness and strength. Post-sintering, edges are smoothed via tumbling to remove burrs, and dimensional inspections ensure compliance with specifications.
Metal Intalox Saddle Manufacturing
Metal variants start with material selection, typically sheets or coils of carbon steel, stainless steel, or nickel alloys. The manufacturing process involves stamping or press forming: flat metal sheets are cut into blanks, then shaped using precision dies in stamping machines to form the saddle’s curved profile and reinforcing tabs. For complex designs, progressive stamping may be used, where blanks undergo multiple forming steps to create the final shape. Welding is rarely needed due to the one-piece design, but some large-sized packings may require spot welding for structural reinforcement. After forming, metal saddles undergo surface treatment: carbon steel is often painted or galvanized for corrosion resistance, while stainless steel and nickel alloys may undergo passivation to enhance their natural oxide layer. Quality checks include dimensional measurements, hardness testing, and visual inspections for defects like cracks or deformation.
Plastic Intalox Saddle Manufacturing
Plastic saddles are primarily produced via injection molding, a cost-effective method for mass production. The process starts with melting thermoplastic resins (PP, PVC, PVDF) in an injection molding machine, where the molten material is injected into a precision mold cavity shaped like the saddle. The mold is cooled to solidify the plastic, then opened to eject the part. For materials like PVDF with high melting points, specialized machines with higher temperature controls are used. Secondary processes may include trimming excess flash (plastic protrusions) and deburring edges. Some manufacturers use blow molding for larger plastic saddles, though injection molding remains dominant for its precision. Quality control focuses on ensuring uniform wall thickness, absence of voids, and dimensional consistency across batches.
Common Quality Control Steps Across Materials
Regardless of material, production includes critical quality checks. Dimensional inspection uses calipers and coordinate measuring machines to verify size tolerances (typically ±0.5mm for key dimensions). For ceramics, density and porosity tests ensure the sintered product meets strength requirements.
metal packings undergo pressure testing or load-bearing checks to confirm mechanical stability. Plastic variants are tested for chemical resistance via immersion in target media. All materials undergo sampling for performance validation, such as measuring specific surface area and void fraction to ensure they meet design specifications for mass transfer efficiency.
Process Optimization for Performance
Manufacturing methods are continuously optimized to enhance performance. Ceramic producers adjust sintering temperatures and holding times to control grain growth, balancing hardness and toughness. Metal fabricators refine die designs to minimize material waste while improving structural integrity. Plastic manufacturers optimize injection molding parameters (temperature, pressure, cooling time) to reduce internal stresses, preventing warping in service. These refinements ensure the final product maintains the saddle shape’s key advantages: uniform fluid distribution, high voidage, and efficient gas-liquid contact.